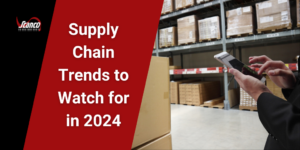
The past few years have been marked by huge changes due to changes in customer demands as well as challenges in attracting employees. Supply chain digitalization has boosted resiliency and productivity.
Supply Chain Trends 2024 and Beyond
Since digitalizing supply chains has been a successful strategy, look for it to continue in 2024 and beyond. The following trends will drive improvements in supply chain management.
1. Cloud-Based Models Remove Barriers to Technology
The major WMS (warehouse management system) brands have either already announced or plan to launch their own cloud-based software-as-a-service (SaaS) models. Moving to cloud-based models gives customers currently using outdated systems the opportunity to upgrade their platforms.
No large capital investment is required. Once the update to a cloud-based system is completed, customers will always have the latest software system.
2. Data Analytics Crucial for Forecasting
Data analytics has established a role in supply chain management. Machine learning is used to analyze previous order patterns. This function includes identifying factors that influence customer behaviors, including economics and the weather. The data is used to create accurate forecasts the company can use to plan for peak times.
3. Information Silos Must be Eliminated
Information silos are inefficient for companies because they create an environment where departments don’t freely communicate with others. Communication only runs in a vertical direction—hence the term silo.
Departments hoarding information have been responsible for information delays and customer service problems. Information silos have also hurt company inventory systems by causing costly stock buffers. They also result in expensive IT upgrades and maintenance.
The solution to this issue is to move the company supply chain workflows onto a single, collaborative business network platform. It’s the best option for cutting across each silo to integrate the information for users from multiple departments.
4. Business Must Maximize All Available Channels
The pandemic forced businesses to rely on all their available channels to achieve success:
- Direct-to-consumer
- Distributors
- E-commerce
- Retail
If one channel is disrupted in some way, the company can rely on one (or all) of the others instead. The business can consolidate demand across available channels.
Software can monitor demand on each channel to keep costs down, increase revenues, and offer exemplary customer service.
5. More Collaboration with Suppliers is the Way to Go
The pandemic definitely taught business owners some hard lessons. One of them was that if there was a risk or an actual disruption to the supply chain, the company needed to be able to respond quickly. The company needed to be in a similar position to respond promptly to surges in demand. Multiple companies were unable to respond to changing conditions during the pandemic due to information delays.
Companies need to continue to improve their supply networks’ collaboration in 2024. Real-time processes and systems will reduce information lags to close to nil.
6. Skilled Labor Shortage Will Continue to Be an Issue
Industrialized countries are having difficulty filling available positions. In some countries, the lack of skilled labor candidates is placing increased pressure on company management. In some regions, approximately a third of businesses that could not fill all available positions also faced the challenge of no applications for open jobs.
Companies that want to attract candidates in this labor market must take steps to stand out from other employers with available job openings. Generation Z candidates are seeking job opportunities where they can use modern IT systems at work.
Employers that highlight their use of technology in their job ads will potentially be able to attract more candidates for available openings. Other strategies that make a company attractive to prospective workers include:
- Education opportunities
- Employer-paid training
- Flexible working hours
- Parental leave
7. Transparency is Increasingly Important
Transparency is required to keep supply chains diversified and resilient. Supply chain managers are required to keep their fingers on the pulse of external issues which may be affecting their company’s supply chain. The economy is still recovering after the worldwide pandemic and is being impacted by current armed conflicts, high interest rates, as well as other issues.
Since the economy is still volatile, companies are being proactive about reviewing their existing contracts. To collaborate in a trust-based manner with all other partners along the supply chain, flexibility is required. Modern IT tools make it easy to share data between parties in real time. Responsiveness is improved and they can make decisions for their mutual benefit more easily.
Scanco Sage 300 Mobile Inventory Provides Multiple Benefits
One situation that is evident from these supply chain trends for 2024 is that companies will continue to face the challenge of achieving better results from limited resources. Scanco Sage 300 Mobile Inventory is an enterprise warehouse mobility application that streamlines counting stock, shipping, and movements inside a warehouse.
- Boosts Employees’ Productivity
Barcode scanning with handheld devices in the warehouse saves time and increases your team’s productivity at work. Barcodes boost employee productivity with:
- Item-based comments
- Item picking
- Inventory counting
- Stock transfers
- Real-Time Inventory Information Using Handheld Devices
Sage 300 updates your computer system each time a team member uses a handheld device to capture:
- Inventory counts
- Item location
- Item quantity
- Item transfers
Real-time inventory totals are updated as new items are scanned into the system.
- Real-Time Integration with Sage 300
Along with the foregoing benefits, Mobile Inventory allows your team to wirelessly import customer details and sales orders. Quickly and easily import the following into Sage 300 ERP:
- Purchase orders
- Received items
- Shipping orders
- Stock counting
- Vendor details
Get these tasks accomplished efficiently at the same time as you keep non-essential staffing costs to a minimum. The app has the potential to improve your bottom line.
To learn more about the Mobile Inventory app for Sage 300 and how it can benefit your business, contact us online, or call (330) 645-9959 to make an appointment with a Scanco Solutions Expert.
The post Supply Chain Trends to Watch for in 2024 appeared first on Sage Warehouse & Manufacturing Automation.